SPOOLMAN-ERMAN
SPOOLMAN-ERMAN is a solution for planning, management of material & construction activities for spool fabrication & erection at shop/site.
- On Cloud
- On Premise
Pipe Spool Fabrication and Erection Software
SPOOLMAN-ERMAN is your go-to software for streamlining every aspect of pipe spool fabrication and erection, whether it’s in the shop or at the construction site. Our powerful software is designed to enhance planning, material management, and construction activities for spool fabrication and erection, ensuring a seamless workflow from start to finish.
Streamlining Pipe Spool Fabrication and Erection
SPOOLMAN-ERMAN is a Pipe Spool Fabrication and Erection software for planning, management of material & construction activities for spool fabrication & erection at shop/site.
Key Features of SPOOLMAN-ERMAN
- Engineering Input
- Cutting & Kitting
- Edge Preparation
- PMI
- Fit-up
- Bay Planning
- Welding
- NDT
- Spool Clearance
- Painting
Benefits of SPOOLMAN-ERMAN
- Increased productivity: SPOOLMAN ERMAN can help you generate piping spool drawings and reports up to 10 times faster than manual methods
- Improved accuracy: SPOOLMAN ERMAN uses a comprehensive library of piping components and fittings to ensure that your drawings are accurate and up-to-date.
- Reduced costs: SPOOLMAN ERMAN can help you reduce your piping drafting costs by up to 50%.
- Enhanced collaboration: SPOOLMAN ERMAN can help you improve collaboration between your engineering, fabrication, and erection teams.
- Efficient Spool Dispatch: Coordinate spool dispatch to the construction site, ensuring timely erection.
- Mechanical Clearance and Insulation Tracking: Track mechanical clearance and insulation processes to avoid delays and maintain compliance.
- Swift Final Clearance: Achieve final clearance for loops and systems swiftly and efficiently.
SPOOLMAN-ERMAN Your Partner in Construction Planning
Watch SPOOLMAN-ERMAN in Action
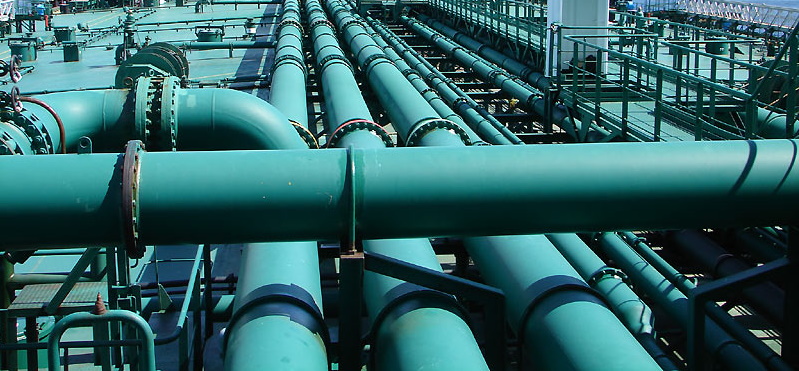
SPOOLMAN-ERMAN Brochure
Read how SPOOLMAN/ERMAN helps you in the management of Pipe Spool Fabrication and Erection
Functionality of Combination Solution
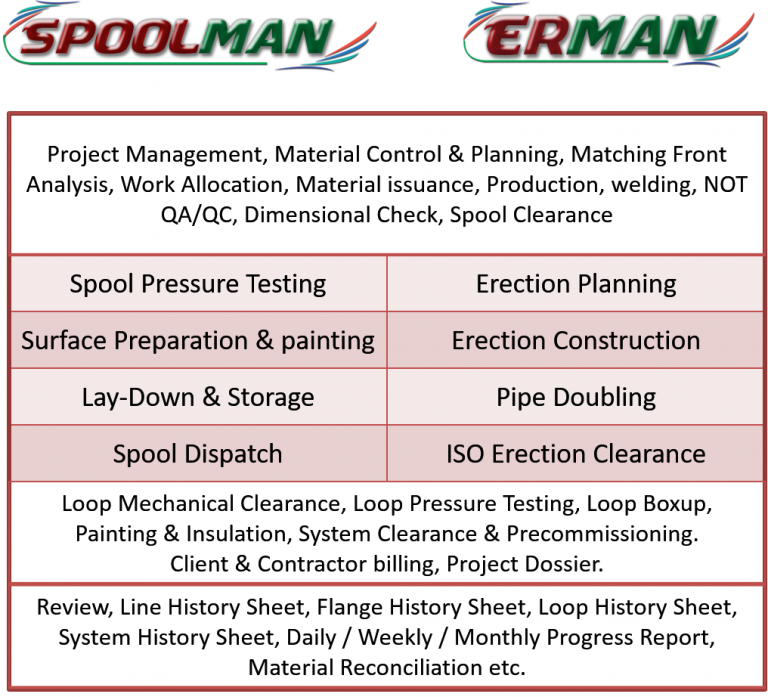
SPOOLMAN ERMAN Deliverables
Seamless Project Execution From Engineering to Planning to Fabrication
We effectively manage your project from engineering and planning to the final fabrication stage.
Our comprehensive approach assures a seamless and efficient process from beginning to end.
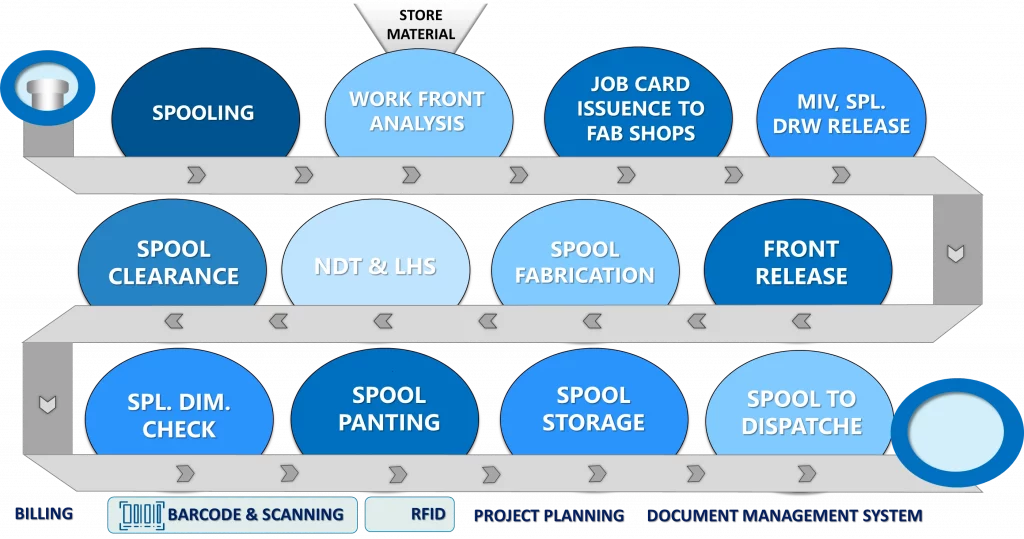
Erection Work Process
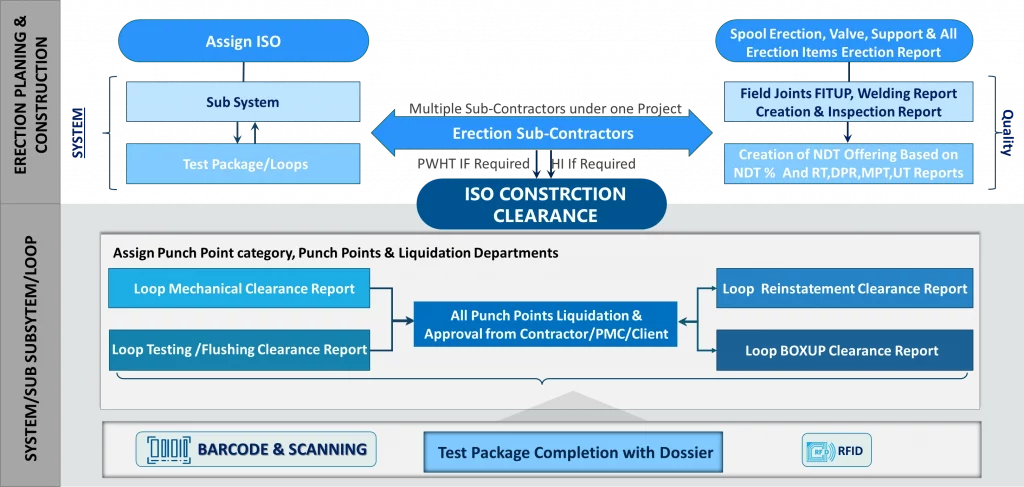
SPOOLMAN Functions
This pipe spool erection software aids in pre-defining various unique phases which a specific spool/line has to undergo in the Fabrication / Erection cycle based on the requirement of project NDT plan, Piping Material Specification, Fluid Code / Service, Paint Specification, AG/UG category etc.
This product controls material in every stage of the work by checking the material availability for Fabrication / Erection of the spool / line, assigning of spool/lines based on the workload available with the sub-contractor, assigning and issuing ma terial to the sub-contractor for the assigned spool / lines, handing over the drawings for fabrication / erection after ensuring material is ready with the sub-contractor for fabrication/erection.
- Fabrication Front analysis:
The Software performs Front analysis for fabrication based on available material at store and material required to fabricate individual spools. The result of front analysis highlights the list of lines, spools & joints which can be fabricated. The results are also indicated through color coding(Green -Completely possible, Yellow -Partially possible, Red – Not possible).
Material constraint list (material required in store to completely fabricate all the partial possible & not possible spools) is generated automatically.
List of balance material available in stores, effective scope & non-effective scope can be generated. Reports of completely possible spools, partially possible spools, not possible spools is generated with spool wise Inch Dia possible for fabrication. - Erection Front analysis:
The Software performs Front analysis for erection based on the availability of erection material at the store and fabricated spools. The associated equipment erection, technical structure installation can also be considered for the erection front analysis.
The result of the analysis is the list of completely possible lines for erection, partially possible lines for erection & not possible lines for erection with possible Inch Meter. Material constraint list for erection item and the status of constraint spools list is automatically generated for monitoring.
This Software helps the planning engineer to analyze the work front availability, assign spool/lines to the sub-contractor based on the subcontractor’s scope of work (like Units / Area / AG / UG piping, Fabrication / Erection, Service etc.) in the project & the current workload available. The work assigned to the sub-contractors are documented with transmittal number & scope in Inch Dia / Inch Meter / Weight allocated against the same.
The Front release assures the materials & corresponding drawings are released to the subcontractors with recorded documents to ensure the released front is available for fabrication/erection.
Before utilizing the material for production Fit-up. Report was created with store material to inspect fabrication shop and PMI (positive material identification).
Fit-up report with parameters like root gap, bevel angle, heat numbers, alignment etc. is recorded. The production activity can be customized & automated through Barcode & Scanning technology with live / batch progress update through WIFI/data transfer
Now, do the fabrication construction progress lively using the mobile applications
NDT (Non-Destructive-Testing)
It is a testing and analysis technique used to evaluate the properties of a material, component, for welding defects and discontinuities without causing damage to the original part.
OGP (Outward Gate pass)
Modules such as Painting, Laydown, and Dispatch are present under outward gate pass.
JOINT BARCODE
- For generating Joint barcode this feature is available in SPOOLMAN( EPCPROMAN SUITE ) ‘WELDING’ Module.
- Spool Barcode And Joint barcode is used for Progressing as well as Tracking location of all feature that is available in EPCPROMAN TNT Mobile application/ RFID Barcode.
- Item Barcode is Used for Tracking Heat No during fit-up time.
RFID read/write software facility in EPCPROMAN
- RFID Tags are used for tracking of the spool.
- Can also be viewed in Google Maps for location viewing with respect to scan time and scan date as shown below