ENGINEERING &
MATERIAL CONTROL
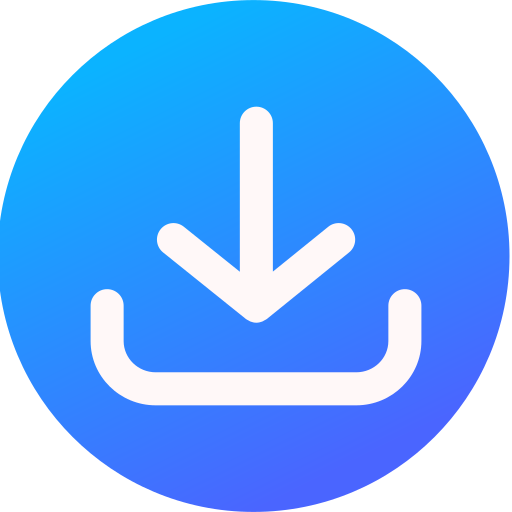
Download Brochure
Discover How ENGINEERING & MATERIAL CONTROL Solution Can Transform Your Projects Download Now !
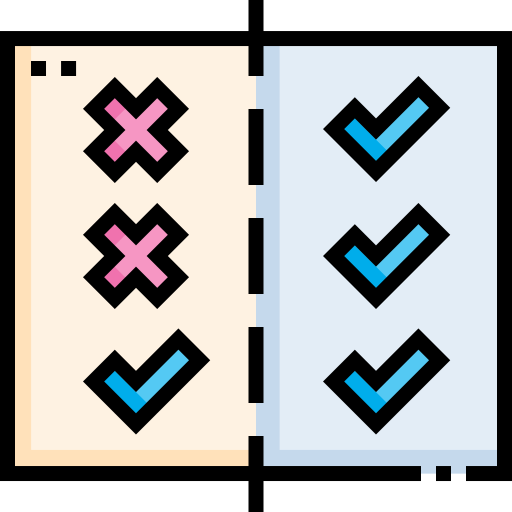
Compare with other Solutions
Choosing the Right Solution for Your Project
Click here to compare
Effortless Material Control: Streamlining Design to Execution with Seamless BOM and MTO Processes
Streamline your projects with Effortless Material Control. Once your design is ready, our system generates a seamless Bill of Materials (BOM) or Material Take-off (MTO), transforming it into a quick requisition for purchase.
What is Material Control ?
- Material Control should ideally be a straightforward process, where a Bill of Materials (BOM) or Material Take-off (MTO) is generated after the design is completed and then used for purchasing materials.
- However, in reality, the different phases of material control often overlap, leading to situations where installation begins before the design is even finished.
- Managing the purchasing of materials while the design is still in progress and dealing with material shortages can be complex, time-consuming, and costly.
- Additionally, controlling sub-contractors during these intermediate phases can further add to the challenges and expenses involved in material control.
- Material control is the system that ensures the provision of the required quantity of material of the required quality at the required time with the minimum of capital investment. It covers the following functions:
- Scheduling of requirements
- Purchasing
- Receiving and Inspecting
- Storing and Issuing
- Stock Control
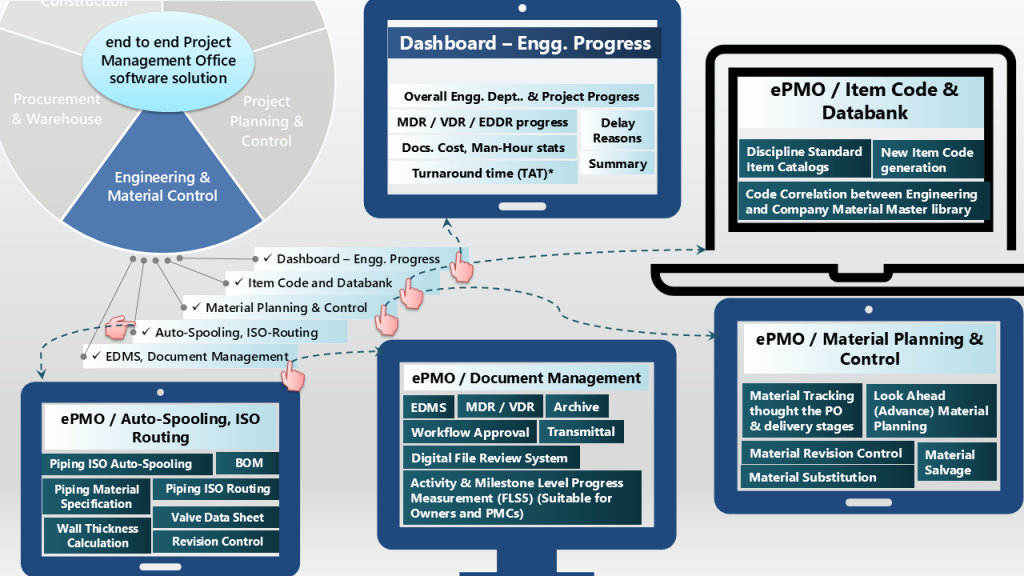
ENGINEERING & MATERIAL CONTROL Solution Includes
1
EGOLDERP
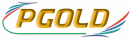
Office Productivity Suite With Resource Assignment Analysis, Time Booking, File Tracking, To Do List, Calenders etc.
PROPLAN
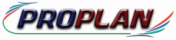
2
Project Network Scheduling, Forecasting and Resource Lookahead Analysis Solution
4
PRODOCS
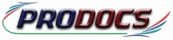
Electronic Document Management System, MDR/VDR, Commenting & Approvals, Workflows & Transmittals
PROCHAL-PROSAFE
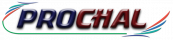
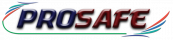
Project Risk/Challenges Management System, Risk Register, Matrix, Heat Map, Mitigation, HSE Management, Compliances, Audits, Meetings
6
PRODASH
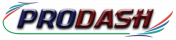
8
Organization MIS, Project MIS, Productivity Analysis, Interactive Dashboards, NLP
13
MATCONTRK

Material MTO evaluation, Substitution, Look Ahead Material Planning, Planning Analysis Reports
ISOMEC 🞹
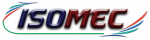
Piping Isometric creation, Material Specification, Valve Data Sheet, Wall Thickness Calculations, Isometric Construction Drawings and Reports
15
Need of Material Control ?
- Planning the proper control of materials and supplies is one of the initial steps in installing a Cost System.
- Material is a significant asset and the largest cost item in most businesses.
- The success or failure of a concern depends largely on efficient material purchasing, storage, accounting, utilization, and control.
- Improper material control can lead to excess stock, tying up capital, and loss through deterioration and obsolescence.
- Shortages of materials can cause production delays.
- Purchasing materials requires specialized skills to order the right quantity and quality at the best price and ensure timely delivery.
- Efficient material control reduces losses, waste, theft, misappropriation, deterioration, breakage, and storage costs.
- Availability of materials reduces idle time in the plant and meets production staff demands.
- Reliable costing information relies on satisfactory records of material issues.
Issues with Material Control
-
No Quote Items : Communication on No Quote Items is not made either by C&P or Project after unpriced bids opening. This delays in procurement of such items apart from confusion at Piping Department
Suggestion : E-mails to be sent to all the concerned the same day. -
Reconciliation of Materials : At present, reconciliation of materials are done by the contractors at the end of project work. This causes great problems in tracking, monitoring & control of materials at contractors end leading to shortage and generation of surplus.
Suggestion : A comprehensive system has to be implemented which will provide real time reconciliation / stock status of each material. -
Offloading of Jobs : During course of piping execution, sometimes, the main contractor fails which warrants off-loading of jobs. In such situation, more than one contractors work in the same zone. This leads to material issue problem.
Suggestion : MTO to be prepared area-wise instead of zone-wise. Offloading of part line to be avoided. - Accuracy of MTO : Correctness of MTO(II) is not in line with requirements. Lot of lines/qty. are added/deleted from one MTO to next MTO. This is one of the main reasons for generation of Surplus. Mismatches in MTO data w.r.t drawings is another big problem. Delay in release of MTO Dump.
-
Identification of Piping Spools & Substituted Items : Due to non-availability of procedure for management, tracking and identification of spools & substituted items becomes difficult. Sometimes spools are lost resulting in additional procurement apart from adverse impact on project schedule.
Suggestion : A proper procedure needs to be developed which may include System / Line-wise stacking of spools. - Excess Issue to the Contractors : There are changes in Qty. from one MTO to next MTO. This is either due to reduction in Qty. or deletion of Lines or both. Adequate material control system is not available to take into account the excess issues of materials to various agencies while generating shortage reports.
- Transfer of Materials across the Projects : To minimise surplus and also to avoid delay in procurement, proper MTO analysis needs to be done before preparation of Material Requisition.
- Delivery Forecast of Piping Materials :In the present systems, month-wise delivery forecast of piping materials is not available. As a result material front calculation against ordered materials is difficult. Besides, equivalent ID/IM against a particular MR/PO is not available in the systems.
Requirement of a System for Material Control?
Systems available with Parascadd
Procurement Management (PROMA)
Major features of PROMA System for Tag & Bulk Items is as under;
- MTO Analysis for probable Substitution
- Generation of Material Requisition (MR)
- Bidders List
- Issue of Request for Quotation (RFQ) to placement of PO
- Monitoring of Manufacturing & Delivery
- Inspection and Expediting
Material Control (MATCONTRK)
Major features of MATCONTRK System is as under;
- Generation of Look Ahead Planning of Material based on Piping MTOs and CDD of Purchase Orders as well as Expediting Reports. MATCONTRK Reports will help in Construction Planning.
Material Control ( AutoSpooling )
Major features of AUTOSPOOLING System is as under;
- Generation of Spool-wise MTO from IDF/PCF & other files
- Generation of Isometrics as well as Spool Drawings
- Taking inputs from PROMA, it makes Material Front Analysis
- Allocation of Materials for Lines as well as for Spools
- Generation of Indents for WHAM for issue of MIVs
- Real Time Reconciliation & Stock Status of Materials
- Optimum utilization of Materials. Scrap generation is bare min.
Warehouse Management (WHAM)
S.No. | SOFTWARE MODULES | DESCRIPTION | SOFTWARE FUNCTION PACKAGES | |||||
---|---|---|---|---|---|---|---|---|
APEXMIS | PROJECT PLANNING & CONTROL | ENGINEERING & MATERIAL CONTROL | PROCUREMENT & WAREHOUSE | CONSTRUCTION & COMMISSIONING | ||||
1 | EGOLDERP (EGOLD-BASE + EGOLD-PLUS + EGOLD-PRO) |
Organogram, Calendar, MOM, Unit Converter, Report Designer,Time Sheet Booking, Job Order Management, Project Charter, Project Photos, Areas of Actions, Project Function Input, Customer Relationship (Sales) Management, Resources Planning & Management, Assets Management, Ticketing System | ✔ 3X** |
✔ 3X** |
✔ 3X** |
✔ 3X** |
✔ 3X** |
|
2 | PROPLAN | Project Network Scheduling, Forecasting and Resource Lookahead Analysis Solution | ✔ | ✔ | ✔ | ✔ | ✔ | |
3 | PROCOST | Cash flow, Cost Estimation & Profit Evaluation, Budgeting & Control (Including Cost Forecasts) | ✔ | ✔ | ❌ | ❌ | ❌ | |
4 | PRODOCS | Electronic Document Management System, MDR/VDR, Commenting & Approvals, Workflows & Transmittals | ✔ | ✔ | ✔ | ✔ | ✔ | |
5 | DATABANK-ICGP | Databank for all disciplines, Item Codification | ✔ | ✔ | ✔ | ✔ | ✔ | |
6 | PROCHAL-PROSAFE | Project Risk/Challenges Management System, Risk Register, Matrix, Heat Map, Mitigation, HSE Management, Compliances, Audits, Meetings | ✔ | ✔ | ✔ | ✔ | ✔ | |
7 | TRACK-N-TRACING | Material, Inventory, Progress Tracking using Barcode & RFID Mobile app | ✔ | ✔ | ✔ | ✔ | ✔ | |
8 | PRODASH | Organization MIS, Project MIS, Productivity Analysis, Interactive Dashboards, NLP | ✔ | ✔ | ✔ | ✔ | ✔ | |
9 | FLS5 | Detailed Functional Scheduling & roll-up progress calculations at Project, WBS, Discipline Activity level | ❌ | ✔ | ❌ | ❌ | ❌ | |
10 | PDIM# | Constructability, Erectability with advanced work packages dynamic information modeling | ❌ | ❌ | ❌ | ❌ | ❌ | |
11 | COCOSYS | Construction & Contractor Activities Scheduling System, Contract Work Items, Scope Quantity Distribution, Schedule & Actual S-Curves | ❌ | ✔ | ❌ | ❌ | ❌ | |
12 | PROMA | Procurement, Manufacturing & Delivery, Tender Management, Vendor Performance Evaluation | ❌ | ❌ | ❌ | ✔ | ❌ | |
13 | MATCONTRK | Material MTO evaluation, Substitution, Look Ahead Material Planning, Planning Analysis Reports | ❌ | ❌ | ✔ | ❌ | ❌ | |
14 | WHAM | Warehouse Management, RFIs, Inspections, OSRDs, Reconciliation | ❌ | ❌ | ❌ | ✔ | ✔ | |
15 | ISOMEC | Piping Isometric creation, Material Specification, Valve Data Sheet, Wall Thickness Calculations, Isometric Construction Drawings and Reports | ❌ | ❌ | ✔ | ❌ | ||
16 | AUTOSPOOL | Automatic Piping Spooling, Fabrication & Erection Isometrics, BOQ, Weld data, Inch-Dia, Inch-Meter / Feet, Pipe Cut-List and more | ❌ | ❌ | ✔ | ❌ | ||
17 | EFA-MFA | Engineering Front & Material Front Analysis, Indent for WHAM, Construction Job Cards | ❌ | ❌ | ✔ | ❌ | ❌ | |
18 | SPOOLMAN-ERMAN | Fabrication & Erection Automation, Progress Monitoring & Reporting for Piping Works | ❌ | ❌ | ❌ | ❌ | ✔ | |
19 | CIVILMAN-STRUCTMAN | Civil & Structural Works Progress Monitoring & Reporting | ❌ | ❌ | ❌ | ❌ | ✔ | |
20 | EQUIPMAN | Equipment Fabrication & Erection Progress Monitoring & Reporting | ❌ | ❌ | ❌ | ❌ | ✔ | |
21 | ENIMAN | Electrical & Instrumentation Progress Monitoring & Reporting | ❌ | ❌ | ❌ | ❌ | ✔ | |
22 | PCAM | Pre-commissioning & Commissioning | ❌ | ❌ | ❌ | ❌ | ✔ | |
23 | PROCCPL | Material, Inventory, Progress Tracking using Barcode & RFID Mobile app | ❌ | ❌ | ❌ | ❌ | ✔ | |
24 | DCAD | Web Digital Computer Aided Design | ❌ | ❌ | releasing soon | ❌ | 🞹 | |
Note: For SaaS (On-Cloud), 100 GB space is default available
for organization accounts up to the active license period. Additional space needs to be
purchased separately.
|